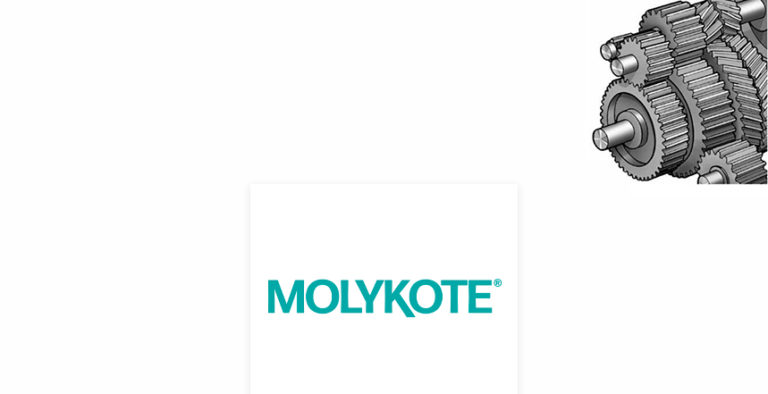
Problem
A food-processing equipment manufacturer was using an ester-containing extreme-pressure (EP) synthetic gear oil in custom-built gearboxes on meat slicing machines. The EP gear oil, which came into close proximity with unpackaged meat, did not meet USDA/FDA standards for use near food. For four years, the manufacturer had been unable to find a food-grade gear oil that could withstand the high operating temperatures of the gearbox, which ranged from 71-82°C (160-180°F).
Application
Helical steel drive gears for a meat- slicing blade.
Product Selected
Molykote® L-1115FG Gear Oil – ISO150 Results
Reduced friction of internal components lowered the operating temperature of the gearbox by 11°C (20°F).
At this temperature, the food-grade gear oil lasted three times longer than the previous gear oil. The plant went from monthly oil changes to a 90-day maintenance schedule. This reduced labor and increased machine up
time, especially since oil changes required 50% disassembly of the gearbox.
Lubricating your gearboxes with Molykote® L-1115FG Gear Oil – ISO150 is a cost-effective way to prevent premature lubricant failure and extend maintenance intervals. Unlike oils made in conventional fractionation processes, the synthetic oil is made by combining smaller molecular “building blocks” to meet targeted performance specifications and to minimize impurities. The synthetic oil reduces friction,
runs cooler, and results in less frequent need for oil changes while providing better protection for gearbox components
Case History: Plant Lubricants
A manufacturer of food processing equipment had developed a custom built gearbox featuring helical steel gears. Designed for a meat slicing operation, the gearbox experienced higher than normal operating temperatures from 71 to 82°C (160 to 180°F). The manufacturer performed numerous tests on available food-grade gear oils and found none that could withstand these operating temperatures. For nearly four years after its inception, the gearbox required an ester-containing, extreme-pressure (EP) synthetic oil, the only gear oil that could withstand the operating temperatures.
However, the oil comes into close proximity with unpackaged meat and was not approved for use with food. Although the non-food grade EP oil operated well within the temperature range of the gearbox, it would break down quickly, requiring maintenance personnel to perform oil changeover every 30 days. This maintenance operation proved to be extensive. Maintenance personnel were required to perform nearly 50 percent disassembly of the slicing mechanism to complete the oil change.
If it were not changed frequently enough, the non-food-grade product might also lead to varnish deposit, which would shorten gearbox lifetime and require
To improve gear lubrication and simplify maintenance, the plant switched to Molykote® L-1115FG Gear Oil – ISO150, a Dow
Corning product. Unlike oils made in conventional fractionation processes, the synthetic oil is made by combining smaller molecular “building blocks” to meet targeted performance specifications and to minimize impurities.
The custom-blended polyalphaolefin (PAO) synthetic oil gives excellent lubrication at high and low temperatures, reduced volatility, and compatibility with equipment designed for use with mineral oils. It conforms to USDA listing requirements applicable to meat and poultry plants, and is qualified for direct food contact under FDA regulations.
Tests during evaluation revealed the Molykote L-1115FG Gear Oil – ISO150 maintained high lubricity even after extended exposure to the demands of the application. Friction within the gearbox was prevented to such an extent that the operating temperature during production dropped 11°C (20°F).
Molykote L-1115FG Gear Oil – ISO150 offers a highly stable molecular structure. The result is a more stable lubricant that lasts longer. Gearbox operating life has been extended three times with this gear oil. Since the manufacturer converted to the food-grade gear oil, end-users of the meat-slicing equipment have not experienced any lubrication proble
ms.
Long Range Benefits
New scheduled maintenance procedures on the gearboxes, which are used on a production basis around the world, involve routine disassembly only every 90 days. On over a thousand such machines, maintenance personnel have found the oil does not require changing prior to this scheduled downtime. Plant management adopted a policy of using only food-grade synthetic PAO products for MRO needs. Although in many cases these products exceed the unit cost of the conventional mineral oils they replace, their superior performance more than makes up for the difference. Standardizing on food-grade products eliminates the possibility that plant workers will confuse one type of oil with another.
Benefits to the Manufacturer
- Better lubrication – food-grade gear oil is cool-running with high lubricity
- Better equipment performance
- Fewer maintenance problems
- Competitive advantage
- Reduced energy consumption
Benefits to Food Processing Plants
- Reduce use of lubricant
- Extend interval between oil change
- Simplify record-keeping for Hazard Analysis and Critical Control Point (HACCP)
- Maintain better gearbox performance
- Extend gearbox lifetime by preventing varnish buildup
- Protect food product from contamination by non-food-grade lubricant